CNC machines are marvels of modern engineering, able to churn out precision parts with ease and speed. However, these machines require a high level of care and maintenance to keep them operating at optimal levels. Regular maintenance can help prevent costly breakdowns and extend the life of the machine.
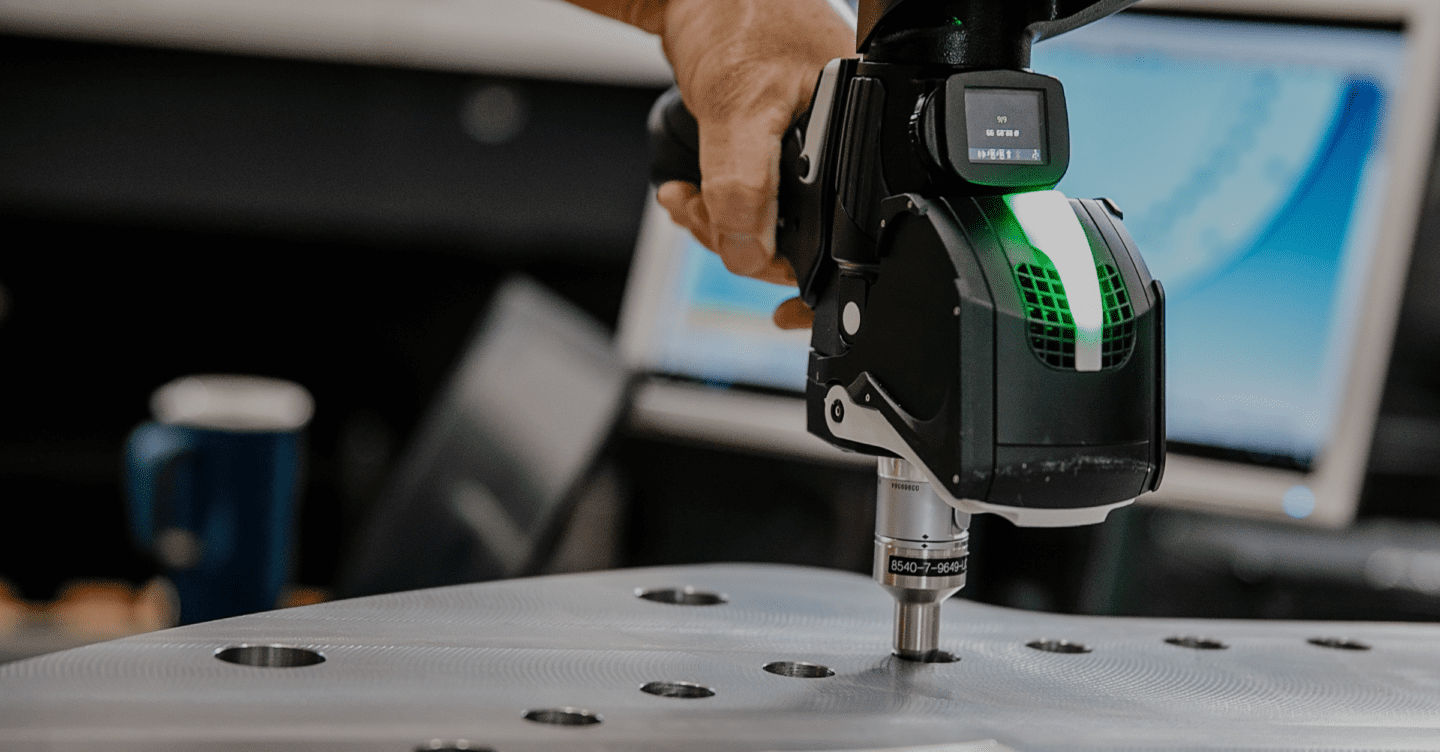
Preventative maintenance is a critical component of any CNC machine’s routine upkeep. This kind of maintenance is meant to be proactive and preemptive, rather than reactive. Instead of waiting for a machine to break down and then fixing it, preventative maintenance involves regular inspections, cleanings, and part replacements to prevent issues before they occur.
At Millcraft Tools, a professional cutting tool manufacturer based in Changzhou, China, the team emphasizes the importance of preventative maintenance for all kinds of CNC machines. “We know that proper maintenance can significantly extend the lifespan of a machine and prevent costly repairs down the line,” says a company spokesperson.
The Basics of Preventative CNC Machine Maintenance
To ensure that a CNC machine remains in top condition, there are several key maintenance tasks that should be performed on a regular basis. These tasks include the following:
1. Check the coolant system: Coolant is an essential component of any CNC machine, helping to keep the cutting tools cool and lubricated. It’s important to check the coolant system regularly to ensure that it’s flowing correctly and that the right mixture of coolant and water is being used.
2. Lubricate moving parts: Moving parts such as spindles, bearings, and slides require proper lubrication to prevent wear and tear. The correct lubricant should be used, and the machine should be cleaned of any excess oil or dust buildup.
3. Conduct visual inspections: Regular visual inspections can help identify any signs of wear or damage early on. A visual inspection should include checking all cables, belts, and hoses for signs of wear or damage.
4. Replace worn parts: Over time, parts such as filters, belts, and hoses can become worn or damaged. It’s important to replace these parts as soon as any issues are identified to prevent further damage to the machine.
5. Clean the machine: Regular cleaning can help prevent buildup of dust and debris, and can also help keep the machine running smoothly.
Benefits of Preventative CNC Machine Maintenance
Performing preventative maintenance on a CNC machine offers several key benefits, making it an essential part of any machine shop’s routine care. These benefits include:
1. Increased lifespan: Regular maintenance can extend the lifespan of a CNC machine by preventing unnecessary wear and tear on parts and helping to prevent breakdowns or malfunctions.
2. Improved performance: A well-maintained CNC machine will operate more smoothly and efficiently, producing higher-quality parts at a faster rate.
3. Reduced downtime: Regular maintenance can help prevent unexpected breakdowns, reducing downtime and ensuring that the machine is always operating at optimal levels.
4. Cost savings: By preventing breakdowns, regular maintenance can help save money in the long run by avoiding costly repairs and replacements.
In conclusion, preventative maintenance is a critical component of any CNC machine’s care routine. By performing key tasks such as coolant system checks, lubrication, visual inspections, part replacements, and cleaning, machine operators can extend the lifespan of their machines, improve performance, reduce downtime, and save money in the long run. At Millcraft Tools, the team understands the importance of regular maintenance and recommends that all CNC machine operators make preventative upkeep an essential part of their machine care regimen.